For standards compliant test procedures & equipment, please refer to Standards Center. For more background theory, please read on...
Introduction
This collection of optic application notes describes how to use a source and meter, or loss test set to measure:
- Absolute power, e.g. the light level coming from a transmitter, or going into a receiver.
- Loss or attenuation, e.g. the relative light transmission efficiency of a device.
- Optical Return Loss.
- Coupled Power Ratio of multimode fiber.
These notes mainly discuss field measurement methods. These can also be used in a factory or laboratory environment, however details of such applications are beyond the scope of this discussion, even if many details are similar.
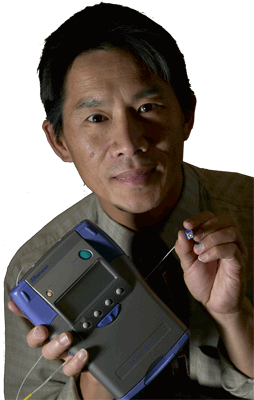
Standard measurement procedures
To ensure uniformity and repeatability of results, there are several national and international standards or Fiber Optic Test Procedures (FOTP) that seek to define a uniform methodology. These are generally under the generic TIA 455 / EIA 455 series standards.
As a rule, for installed systems, the standards encourage attenuation measurement using the bi-directional method at two wavelengths, one of these being the operational wavelength.
In general, there is good accord between standards on each FOTP, however slight differences do exist with some of them. Since these any fiber optic testing procedure is subject to update, it is recommended that where conformance is mandatory, the user contact the relevant standards body.
For further background information: A2 Loss Measuring Concepts
How much verification & validation?
Installed system evaluation can be broadly divided into 3 categories:
- Certification
- Maintenance
- Restoration
Installation certification is the most complex, being designed to ensure the quality of the completed system and provide documented proof of this quality. This is typically performed after cables have been placed, and joints have been made.
Maintenance checking is less complex and is designed to provide early warning of possible failure.
Restoration is the least complex, although it may be performed under adverse conditions: Find and fix the fault, verify the repair quality, restore the system.
Assurance activities should be examined overall in terms of risk management and cost benefit. This includes costs incurred by: Installation, maintenance, system down time, service reliability guarantees, lost revenue, and general conformance to stated quality objectives.
The single direction loss measurement method is initially quicker and cheaper; however, the bi-directional method is preferable for more reliable overall characterization, since it significantly reduces the likelihood of rework and associated cost blow outs.
The Kingfisher KI734x & KI774x series two way LTS perform dual wavelength, bi-directional loss and ORL measurement with less effort than a basic measurement using simple gear. If there is any volume of work, this is clearly today's preferred solution since it achieves a full characterization with the least effort.
An OTDR measures loss by using a fundamentally different method to a source and meter, since it works by indirect deduction, whereas source and meter perform a direct measurement. More information: A15. When to use an OTDR or LTS
Procedures need to take account of record keeping requirements and traceability, which can cause a significant administration overhead. Kingfisher’s KITS™ Excel based reporting program is ideal for this purpose. Using this program and a suitable two-way instrument, one mouse click and a few seconds is all it takes to record the bi-directional loss and ORL at two wavelengths.
Procedures and instrument selection will be affected by a combination of capital availability, labour, skill, and technical requirements. It will also be affected by the size, work practices, and division of labour of the organisation. Loss checking is a time-consuming process, but the collection and maintenance of a records database can be an even bigger issue. It is worth examining the whole issue by looking at required record keeping objectives, and then work backwards towards the field measurement practices.
Who should be doing this?
This can be put another way: Who can I trust? This is the foundation on which all technical inspection rests. Ultimately, some form of auditing is also desirable.
If management place expectations on staff which result in errors, short cuts and lies, then no attempt to prevent this happening can be successful. For example, a technician can always make the same measurement 12 times to make it look like 12 different results, even if the apparatus is perfectly engineered to prevent any possibility of tampering with data.
Questions of Management Structure, appropriate Professional Qualifications, Company Policy, Accurate Measurement Procedures, Working Environment, Training, Asset Management, Documentation, technician professional development etc are central to the management of a professional measurement environment such as exists in a Traceable Calibration Laboratory. The same general principles can be extended to all measurement situations.
See also: A13. Practical Quality Control of Fiber Optic Measurements
Measurement uncertainty
When estimating measurement uncertainty limits, a confidence level of 95% is usually applied, e.g. the measurements will be within the limits 95% of the time.
Measurement uncertainty needs to be established. Theoretically, it comes from:
- Source initial wavelength tolerance, and power / wavelength drift over time / temperature
- Meter initial calibration accuracy and accuracy over time, temperature, range (linearity), connector type and wavelength.
- Connector loss uncertainty.
- Mismatch between system operating and evaluation conditions (particularly for multimode systems).
When interpreting uncertainty or stability specifications, a reference to a value always implies a + and - value and will also include rounding effects. Therefore, a stability specification of 0.1 dB allows a variation of ±0.15 dB, or 0.30 dB peak - peak. A specification of 0.15 dB will allow ± 0.155 dB, or 0.32 dB peak - peak, and a specification of 0.10 dB will allow ± 0.105 or 0.21 dB peak - peak.
When using the bi-directional method, note that an additional source of error is the incorrect practice of averaging dB loss values. It is not mathematically correct to average dB values. For more information, see A14 Improving Attenuation Measurement Accuracy
It is also true that in many practical instances, user training is the limiting factor.
Effect of connector loss uncertainty on measurement technique
It is critical to understand the way connector losses vary and affect measurement uncertainty. Connector losses vary with wear, time, temperature, and each time a connection is made. In multimode systems, connector loss may vary with position in the system, depending on modal distribution. A statistical mean and standard deviation approach (based on manufacturer's specifications) should be used to estimate the introduced uncertainty, verified by practical trials on a sample of the actual terminations used.
A common cause of errors is poor work practice in relation to connector cleaning. Connector tips should be cleaned with a lint-free cloth or tissue before each insertion. An indispensable item is a ' stick ' cleaner which can clean inside a mounted through connector or device receptacle.
An inspection scope should be used to check the quality and cleanliness of connectors. These microscopes are available in a wide range of price and performance. As a rule of thumb: don't get more magnification than required, and don't get less:
- A cheap x100 unit is not adequate for good work.
- A good quality X200 unit is ideal for general use.
- A good quality x400 unit is ideal for a QA laboratory.
Connector loss uncertainty always affects loss measurements, and the main measurement techniques are defined by their use (or not) of connectors.
Note that the connection into a meter generally has no loss, (although there can be calibration offsets which depend on ferrule material and polish type). The source connector behaves like a normal connector.
Note: it is good practice to check your patch leads by reversing them (e.g. the other ends go into the through connector), and re-measuring the reference value, which should only deviate within the expected tolerance of your connectors.
See A5 Optical Connector Characteristics
Effect of wavelength
It is normally considered mandatory to measure loss at the nominal operating wavelength of a system, since loss is generally wavelength dependent.
It is essential that the meter be set to the same wavelength as the source otherwise serious errors may result.
Also, there is a wavelength tolerance on most emitters, typically 30 nm, which may lead to some mismatch between the measured loss using a measurement source, and the loss seen by the installed system.
See A18 Which loss Measurement wavelengths do I need
Battery operation
An often-overlooked parameter.
Not all battery types are readily available in different counties.
It is important that at least one full day's work can be achieved on a set of batteries. Within the industry battery operation times vary circa 10 to 1200 hours.
Also consider any required instrument warmup time. Most but not all sources have a warmup time of about 20 minutes each time the wavelength is changed.
Rechargeable batteries, whilst initially seeming to have an advantage over non rechargeable types, typically have a higher internal discharge rate and smaller capacity leading to shorter instrument ‘on time’ which tends to negate their usefulness. For this reason, Kingfisher KI7000 instruments use standard ‘C’ cells.
Effect of measurement gear
For information regarding the effects of Measurement Gear, refer toe:
A8. Source Characteristics
A9. Meter Characteristics
Effect of fiber type on measurement technique
For multimode measurements, a method of defining the modal distribution is required as part of establishing the reference condition. See also A4: Modal Distribution
Measurements on single mode systems are typically faster, easier, and more precise compared to multimode measurements, which are more prone to drift, noise and lack of repeatability.
Some very old or specialised fibers may require the use of a cladding mode stripper to remove cladding modes. One way of achieving this is to strip the plastic coating off a few cm of glass, and immerse this in Methyl Salicylate, a (smelly) chemical that is easily available from most chemist shops.
For all measurement work, it is important that your patch leads match the target system.
One reference lead or two, or three?
How many reference leads?
There are frequent (heated) industry discussions about how many reference leads should be used when taking a reference.
Mathematically, the two-reference-lead method is theoretically correct. So, this is used in the examples.
The other methods may produce valid results for situations. The situation can be summarized as:
- The one-lead method adds one extra connector loss to the theoretical insertion loss.
- The two-lead method produces the theoretically correct insertion loss.
- The three-lead method subtracts one connector loss from the theoretical insertion loss.
Some sections of the industry in the building cabling sector have identified that they can work faster using a one lead method, and they are also using this to add an extra connector loss to the measurement, to compensate for an absent drop lead. In other words, they are measuring the loss that will be seen by an attached modem when it is ultimately attached by a short drop lead.
In addition to fundamental loss measurement, there are other issues that can also be addressed by smart use of jumper leads:
- Are my jumper leads in good condition? This can be verified by zeroing the meter, then reversing the jumper leads and checking that a consistent result is obtained. Failed jumper leads are major cause of acceptance problems.
- Does my jumper lead core diameter etc match the system being tested? This is where the "3 reference lead" method is helpful, providing of course that the middle lead is truly representative of the system being measured.
- Are there possibly mismatched fibers in the installed system? This may not be detected by the one lead method but will be discovered by the 2 / 3 lead method.
The following example can be used to settle a common dispute about insertion loss accuracy: If you are not interested in this issue, please skip it!
Suppose I make a transmission span based on say 100 patch leads joined end to end, all with the same insertion loss. I don't think anyone would disagree, that if I remove one patch lead and re-join the other 99, the reduction in loss would be the insertion loss of the removed patch lead. This simple observation implies using EITHER two reference leads and a through connector, OR possibly one lead and then subtracting one nominal connector loss value from the result. Any other method is mathematically incorrect, since in this example it will lead to massively over-stating the loss of the 99 joined patch leads.
Practical measurement examples
More information